By Walter R. Stahel
The Product-Life Institute GenevaThis case study was first published in 1989 in German as part of the book:
Stahel, Walter R. (1989) Langlebigkeit und Materialrecycling - Strategien zur Vermeidung von Abfällen im Bereich der Produkte; Vulkan Verlag, Essen; ISBN 3-8027-2815-7. second edition 1992.A partial English translation was published by the R&D office, U.S. EPA, Washington D.C.
Low-polluting small appliances, price range: 100 to 999 DM.
The first two sections (actual manufacturer’s case study) were prepared in conjunction with the manufacturing company mentioned. The research group takes full responsibility for the product case study.
Description of the Product Examined
Two-handed angle grinder (ZHWS), professional power tool program 1990/91; with electrical cord for power connection, without sanding disks, manufactured by Bosch in Stuttgart, Germany.
In its application (cutting, sanding, roughening, brushing; dry and wet processes) and its application area (building, metal working, dressing rocks, automotive industry; workshops, building sites), this is a universal tool.
Market Description
The power tool market lives on product wear (units used in long-term commercial operation) and product innovation (replacement or redundancy market (kept in reserve as a second tool)); potential market saturation is overcome by the production of improved units or the development of special versions.
Market Volume
The German market for power tools has a volume of about 1.35 billion DM, of which more than half comes from domestic production. The angle grinder occupies about 13% of the power tool market; the two-handed angle grinder (the tool studied here) has a market share of 3.2%.
Most of the German production of power tools, to a value of almost 2 billion DM, is exported; German manufacturers represent about 19% of the world market.
Existing Studies of the Product. Power Tools
§ Gehrmann, F. (1986). Design and Value-Maintaining Recycling of Inexpensive Technical Consumer Goods, Represented by the Example of Small Household Appliances.
§ Steinhilper, RoIf (1988). Product Recycling in Mechanical Engineering.
Wear Parts
The wear parts are mainly the carbon brushes (life of 100-200 hours) and the commutators or switches (200-250 hours); the other wear parts—drive unit, bearings, switches, motor anchor—are designed to have a standard theoretical technical life, but this may be reduced to a fraction of its length when the tool is used for certain applications such as cutting rock or metal, if the resulting dust is sucked inside the unit.
Useful Life
It is not possible to give data on the effective life of this tool (average, minimum, maximum) because of the great variety of applications in terms of usage and time.
The power tools made by Bosch are designed to have a long life; in the design contest held by Miti in Japan in 1989, Bosch won prizes for five of its power tools and thus was among a small group of ten foreign companies whose products won prizes. The durability of Bosch power tools is also demonstrated by the fact that in the exhibits and books of the Design Center in Stuttgart on “lasting design” (i.e., on the market for at least 10 years unchanged), each time several of these units are listed.
Possible Future Technological Advances
Power tools consist mainly of a motor and the tool. Technological advance in motor design is possible in the direction of wear-free squirrel-cage motors with electronic control. Technological advances in the tool are less significant, as they can usually be retrofitted. (See Table at the end of this case study.)
1 Actual Status of Current Production and Distribution Development. Design, and Manufacturing
This tool is designed for a theoretical useful life of at least 600 hours (in lab operation) according to test VDE 0740. Since this tool is sold internationally, it also satisfies European and American standards.
In principle this tool is designed for ease of maintenance and of dismantling; worn parts can be replaced without damage to the tool. In its design there is a clear distinction between maintenance measures that the consumer can carry out (replacement of brushes) and those that the service department of the manufacturer should carry out (replacement of the electrical cord, re-turning of the commutator-switch). Except for changing the brushes and possibly re-turning the commutator, this tool is maintenance-free for its theoretical useful life.
The choice of materials is made according to the criteria of cost and material use; disposal, including recycling of materials, is not a priority in the material selection (which explains the use of more than ten different plastics), but it is in the design (example: housing screws screwed directly into plastic, without sleeves). Table LB shows the percentages of materials used in this tool.
Distribution (as far as the point of sale)
The distribution of professional power tools is handled exclusively by hardware stores. This tool carries a 6-month warranty on materials and lack of defects, according to BGB (Bürgerliches Gesetzbuch, or German Civil Code).
Customer Service (after purchase)
Customer service for this tool is handled through a central workshop in Willershausen (south of Hanover) and a network of 120 free customer service centers. At present the volume of repairs is distributed about 50/50 between the local customer servicemen and the central workshop; the latter also does all work required under warranty. The central workshop is available both to individual customers and to the hardware trade; units are delivered by truck and are returned to the sender within 48 hours by truck. The central customer service office works on about 700 electrical tools per day, 40% of which are still under warranty (6 months). Hardware stores currently lack the technical competence to make repairs.
The design of the tool offers a high degree of repairability and permits the reconditioning of components several times (mainly the commutator), although in the view of the manufacturer this should only be done at the central Bosch workshop in Willershausen. One reason for this is the large number of replacement parts (about 19,000 for all power tools), which only the central workshop has on hand. However, all replacement parts are available to all potential buyers (local customer servicemen, hardware stores, and private individuals).
Until a few years ago the Robert Bosch company operated a carefully worked out exchange and depot maintenance system, but this was given up in favor of the central workshop in Willershausen. Two factors were instrumental in bringing about this change: a switch in material, and the quality of the local customer servicemen:
§ The tool’s housing, formerly of aluminum, is now made of plastics, which provides greater user safety (protection against electric shock). These plastic housings cannot be repaired or refurbished during rebuilding or reconditioning (dent-removal, polishing, respraying) as the aluminum housing could. Furthermore, the plastic housings met with distrust among consumers that could only be overcome by replacing the housing with a new one, which for economic reasons is not feasible, however.
§ The repair cost estimates at the store or at the local service centers had reached a range that was no longer acceptable to the manufacturer and that could not be influenced. Thus the profitability of exchange maintenance (and thus of the company) was seriously threatened.
This argument should be taken into account in an alternative solution, “equipment rental” (see Section 1.4). Statements made in earlier articles (including Steinhilper (1986), Rebuilding of the angle grinder) should also be revised in this respect.
The reader is reminded that responsibility for Section 1.2 and those following (product case study) lies exclusively with the research group.
2 Actual Status of Disposal
There is no “end-of-pipe” customer service. The hardware store acts as seller, and sometimes as the external arm of the central workshop, but is not a take-back and disposal agency for power tools.
The central workshop of the manufacturer, on the other hand, is ready to dispose of power tools that the owner no longer wishes to repair, at its own cost by way of the scrap trade (which uses shredders equipped with a flotation separation method). This disposal makes a positive contribution and allows materials recycling of the iron and non-iron metals; however, shredded plastics can no longer be recycled and become part of the shredder waste. It is assumed that most power tools are disposed of today in the household trash.
Strategies for Waste Prevention
We must account for the fact that the different types of power tools (for do-it-yourself, professional, and industrial use) are subjected to a greatly varying degree of intensity of use (number of operating hours annually) over their theoretical technical life. This has led to three different designs with greatly differing theoretical useful lives: units for the handyman, 200 hours; professional units, 600 hours; industrial units, 2,000 hours (in lab operation).
Basic Strategy 1. Long-Life
A. Long-life products
The power tool as a long-life product can be found today in the form of industrial tools:
these are largely maintenance-free thanks to a motor with a squirrel-cage design (without anchors and brushes), which also lends itself to recycling (aluminum instead of copper, no drip resin). These units run only on a 3-phase high-frequency (300 Hz instead of 50 in normal power) and therefore can be used only in plants with the appropriate equipment.
B. Product-life extension of the entire product
B1. Reuse: As there is no information available about the condition of the units before they are thrown away, we cannot discuss their reusability.
B2. Repair: As there are no useful sales statistics available for wear parts such as brushes, we cannot determine the extent to which repairs such as brush replacement are carried out today. Thus it is also not possible to break down this information according to central, local, and do-it-yourself percentages..
From the case study on the service sector we know that repairs of power tools are regularly carried out at “repair shops.”
B3. Rebuilding: The motors, anchors, bearings, switches, and power connections can be replaced.
B4. Technological upgrading: From the list of technical innovations in the last 10 years (see Table 1.A), we can see that the following upgrading of older units would be possible:
§ Without maintenance work: the new quick-fastening system SOS “click”; since it is compatible with power tools made by other manufacturers, any upgrading rate for the tool under study cannot be derived from sales figures.
§ Associated with maintenance work: replacement of fan wheel made of aluminum with one made of plastic; free replacement of old brush mount with new one (only through the manufacturer’s workshop); these options are not offered.
C. Product-life extension of components (second-hand components)
§ This option is not exercised at the central workshop, as otherwise the entire storage requirement and bookkeeping would be doubled, which is not economically feasible.
§ Local repair shops and do-it-yourself: It is entirely possible that this option is utilized locally, but there are no statistics available. The trend on this is probably negative, however, parallel to the decreasing number of free customer service centers in Germany. Possibilities are:
C1. Reuse of used components or part groups such as housing parts, possibly the stator and anchor package with axis.
C2. Repair of components such as housing pans and electrical cords/cables.
C3. Repair by module replacement of components such as motors, commutators, and drive units.
C4. Technical upgrading of components (retrofitting of dust protection by installing the double labyrinth: scarcely possible, as the expenditure would be too great).
V. Waste-preventing distribution strategies
V1. Operational leasing and rental: exists today in certain hardware shops and do-it-yourself centers.
V2. Shared use: exists today in isolated instances, such as in the “Sharing Communities” in Switzerland.
V3. Sale of the service of quality control, instead of the replacement sale of products; not applicable here.
Basic Strategy 2, Materials Recycling
Problems occur in materials recycling mainly as a result of compound materials, combination parts, toxic waste, lack of identification of materials, lack of collection organizations, and lack of recycling technologies. From Table 1.B we can see the precise percentages of materials.
§ Compound materials are present in the form of the housing made of glass fiber-reinforced polyamide (PAGF).
§ Combination parts are present in the form of the motor anchor (copper windings, iron core, drip resin), and the switch (many noniron metals and plastics, drip resin).
§ Toxic waste: this product is free of heavy metals (except for the switch).
§ The current units do not have any special identification of the materials. This will be introduced beginning with the model year 1991 in accordance with the German Institute for Standards; however, it is concealed (i.e., it can only be seen once the unit is taken apart).
§ There is currently no separate collection organization for power tools. The disposal of these products is unknown, but it probably occurs with the household trash by landfill or incineration.
§ Lack of recycling technologies (this unit consists of roughly 58% steel, 26% nonferrous metals, 16% plastics, and other materials):
- Power tools that are delivered after careful sorting and in certain amounts to the scrap dealer can be recycled through specialized shredder and separation (flotation) methods, by as much as 70% to 80% (metal parts) quite profitably. However, in Germany today there are only a few facilities capable of separating copper and aluminum scrap. The technology for separating shredder metal scrap is also very environmentally polluting (lead) (see Section 1.7, no. 2).
- The remaining 20% to 30% (plastics) can be recycled only if the unit is disassembled and the plastic waste is ground separately. Mixed plastics or plastics that have passed through the shredder can be incinerated in the form of shredder scrap or can be dumped in landfills if suitable systems are available that are equipped with filters.
Reasons for Shortened Useful Life (obsolescence)
The changeover to the European 230 V power might lead owners of older electrical appliances to believe, for incorrect safety reasons, that they must discard their appliances. This would then shorten the useful life of the tools. To avoid a campaign for sales promotions in the trade, for the same reasons, it might be advisable to inform the customers as a precaution.
Unsatisfactory quality of components such as switches might result in the unit being thrown away long before it reaches the end of its theoretical technical life, as a result of loss of confidence on the part of the user or as a result of high general costs at the central workshop. The only remedy for this is to improve key components that are susceptible to flaws; these are usually easy to discover through statistics on the work done under warranty. It is possible that institutional obstacles such as technical standards, or business obstacles such as suppliers with quasi-monopolies, might hinder such improvements.
The increasing importance of central workshops and their increasing transportation costs, together with the phenomenon of the “repair cost scissor” (increasing labor costs and decreasing appliance prices), means that in the future appliance quality will have a growing influence on the effective product life and thus on the waste volume. It is to be expected that as a result of the multiplier effect of the general costs of a repair (packing, transportation in both directions, cost estimate, presentation of two bills by the repairman and the dealer), small appliances with only one component of inadequate quality will soon become throwaways (the “pars pro toto” syndrome). Thus, component quality will possibly become a central topic of waste prevention for small appliances. Performance standards that also lay down minimum product life can become a useful tool in writing waste laws.
4 Suggestions for Alternatives to the Actual Status
(see Table at the end of case study) One objective of these case studies is to define solutions that:
One objective of these case studies is to define solutions that:
§ Are technically and commercially conceivable
§ Are feasible for a manufacturer
§ Are desirable or at least acceptable to the Robert Bosch Company, taking into account the technical and commercial possibilities for waste prevention in the present situation.
The solution that satisfies these three conditions is called the “primary option”; solutions that satisfy the first two conditions are called “options.”
Primary Option. Materials Recycling (basic strategy 2)
In view of the complexity and variety of their uses, the value of the raw materials, and the currently predominant dumping in landfills of power tools that are thrown away, the strategy of materials recycling offers itself as the most tempting alternative solution. This solution requires:
§ In production, a product design that is appropriate for recycling (according to the German Institute for Standards), a restriction to the smallest possible number of materials, which also have to be recyclable, the elimination of compound materials, and externally visible material identification marks (in the case of the tool studied, these conditions are largely satisfied).
§ In disposal, the existence of a (mandatory) return or take-back system that guarantees disassembly of the units into lots of the same materials, or into material mixtures that can be mechanically separated, and that then sends these to qualified recycling operations.
Disassembly: These units consist 95% of valuable recyclable materials; however, reclaiming the materials requires partial disassembly of the units (separation into plastic parts and aluminum parts (housing), iron-copper mixture (mechanics), and special waste (switch)) as long as the shredder companies do not have flotation systems available for separating the various nonferrous metals. The plastic parts have to be ground separately and must not go through the shredder (see Table).
Choice of disposal path: The disposers could be either the store (take-back requirement, “take-to” system) or the county districts (containers, “take-to” system). The main difference between these two systems is that the costs are taken over either by private economy (manufacturer/store) or by the government. Thus, the choice of the system is political in nature and is not the subject of this case study. In the other options we also find that take-back by the store sometimes opens up further options for extending the product life of the tool and can be reinforced by incentives (e.g., deposit). Since this form of disposal may be profitable, a solution of this type could give stores ideas for new activities in take-back trade.
Separate disposal of power tools through the county districts would probably, because of the waste volume, only be sensible if the program were extended to include all small electrical appliances (such as hair dryers, kitchen appliances, garden tools); incentives for return would be hard to incorporate in the system. Certain private disposal companies (see case study, service sector) are currently already equipped to carry out these activities inclusive of plastics recycling (regranulate). As the Marburg project has shown, the disassembly required for materials recycling could be combined with measures for waste prevention through product-life extension of electrical appliances, in the context of government policies in the area of job creation.
Options for Intensifying Use
Most power tools owned by do-it-yourselfers suffer from the phenomenon of “slow-motion use,” i.e., a low intensity of use over a long period of time, which means that many tools probably never reach the end of their theoretical technical life. Precise information on this could only be obtained by installing meters in the tools to count the operating hours. This phenomenon can be overcome by a strategy of intensification of utilization.
Multiple use through rental systems (strategies Vl/V2): A fleet manager (owner of a fleet of tools) rents these out to users for short, medium, or long periods, for example, in the form of an operational lease of new equipment (exists for power tools in Great Britain). This form of rental could be implemented by the manufacturer via the hardware dealers, or by the mail order companies all over the country through their catalogs and mail delivery, or by public institutions in a “tool library” system similar to public libraries (which according to this system are the “fleet managers” of books).
Here we should take note of the argument of the problem of refurbishing tools with plastic housings, which led the Bosch Company to give up its exchange maintenance system. In Germany this option may sometimes only lead to limited success.
Multiple use through user associations (also called sharing associations: strategy V2): The individual ownership and the use of consumer items that are not used daily are separated from each other in that these products are either lent out among the association members, or owned and used jointly by user groups (example: “share-corn” associations in Switzerland).
Options of Product-Life Extension of Entire Product
“Donation” (“away-grading”): Tools that have become obsolete because of technical advances can be used in another part of the world where this technical advance has not yet occurred.
Fleets of used appliances: Incentives can be used to encourage the return of old tools instead of keeping them as “redundancy options”; these tools can then, for example, be commercialized further by the hardware stores as rental tools without incurring the investment costs for a fleet of new products.
Keeping spares (redundancy): A large number of second and third tools are kept in many households “in reserve,” especially tools used by do-it-yourselfers. This delayed disposal represents a potential for donation (“away-grading,” see above), but might also, in the event of a technical advance on the system level, cause old tools to be thrown away en masse for reasons of obsolescence.
5 Improvements
Measures on the Part of the Manufacturer During the Transition from the Actual Status to the Alternative Solution. Primary Option
Production-based: Reduction of the number of different types of plastics used from over ten to one or two (e.g., polyamide with and without glass fiber reinforcement) for all nonelectrical parts (enameled wire, drip resin, etc.).
Distribution-based: Re-education of distribution paths (hardware stores) from “points of sale” to “points of sale and take-back,” with knowledge of the scrap business and recycling market.
Further Measures on the Part of the Manufacturer Toward Low-Waste Products
Production-based: Technical improvement of key components such as switches that cause the failure of the tool already during the warranty period and later, in view of the “repair cost scissor” (see end of Section 1.3), run the risk of shortening the effective life of the tool.
Other Measures to promote the application of basic strategy 2, materials recycling.
6 Business Evaluation of the Primary Option
One goal of the case studies is to investigate the effects of the primary option on business and the economy. Changes in waste volumes and their toxicity and the consumption of resources in production, distribution, utilization, and disposal are taken into account.
Primary option, power tools case study: basic strategy 2, materials recycling: separate return of old tools via take-back by the sales outlets, sometimes with packaging, and/or return with separate waste collection; partial disassembly (into parts made of one pure material) and materials recycling via shredders (thick line in Table 1.C at end of case study).
Our business evaluation compares the following two variations (see Table 1.C at end of case study).
§ Actual status: disposal with household trash.
§ Primary option: separate collection of old tools combined with materials recycling.
The power tool consists of ferrous and nonferrous metals as well as plastics (for precise figures see Table 1.B). If they are delivered as pure materials after disassembly (clean and separated), then they can be reprocessed using existing recycling technologies. The manufacturer could make this even easier. The reduction of the number of plastics used from about 20 to 2 increases the production costs only by a few pennies, which is offset by the higher quality of the materials and the possibility of using recycled materials. There are compound materials (e.g., switch) and compound parts (e.g., pole shoe) present in the tool.
Possible disposal paths are
a. Disposal by the manufacturer: already the norm today for damaged units sent to the central workshop that the owner decides not to have repaired.
The manufacturer’s service workshop already passes on to specialized disposal companies tools that are sent in but are no longer worth repairing. On the other hand, the incentive of component reuse may be lacking in a developed system of retrodistribution. We are working in the field of small appliances where the monetary value of components or used parts cannot be harnessed as it is in the auto repair industry.
b. Disposal by the hardware store (possibly passing the tools on to the manufacturer): The hardware store is not (yet) thought of today as a return and disposal point.
If we imagine a scenario “Materials recycling through hardware stores” and if we look at the activities that precede and follow the take-back of used tools (take-to system) and the distribution of the recycled materials including the disposal of the residues, then the problem of the distance between the (hardware) store and the consumer arises. If we disregard incentives and government take-back requirements, it might be questionable whether the consumer will play the game. On the other hand, the hardware dealer would achieve his goal if he takes the same path as the manufacturer (delivery ~? the used tools to specialized disposal companies). Further analysis might, under the current limiting conditions and legal requirements, supply guidelines for a feasibility study of this scenario. It could be expanded in a subsequent step by establishing new legal instruments.
c. Separate disposal via the municipalities or county districts, as a supplement to existing collection of valuable materials.
The scenario “Disassembly by the hardware dealer and comprehensive materials recycling” could be supplemented by separate collections by the county districts. However, the aforementioned political decision relative to the strict application of the waste-producer principle would have to be considered.
The business evaluation of other options such as utilization intensification by means of multiple use in rental systems or user associations, or increasing the effective life of the appliance by reducing its susceptibility to breakdown (i.e., higher quality of key components) is not pursued here. In the latter case, the manufacturer has already set himself the goal of improving by a factor of 3 or 4 the ratio of “sales to returns under the warranty.” Detailed cost-benefit analyses relative to a strategy of durability are already in progress and include diagnosis and therapy.
7 Environmental Aspects of the Primary Option
How does the return (separate collection) of used tools with subsequent disassembly and comprehensive recycling of materials (primary option) fare in comparison with dumping and incineration from the point of view of the amount of waste, the consumption of resources, and the emission of pollutants?
Waste and the Consumption of Resources
1. At present most power tools are disposed of via the household trash either by dumping or by incineration:
Amount of waste 4.82 kg = 100% (certain reduction of waste for incineration (plastics))
Consumption of resources 4.82 kg = 100%
2. Disposal via shredding of the entire unit without disassembly at a modern plant with flotation separation (e.g., used units at the central workshop of the manufacturer) permits the reclamation of most of the metals.
Waste reduction for the tool studied (ZHWS), about 80-84%,
for an average power tool, about 65-67%
Consumption of resources for the tool studied (ZHWS), about 16-20%,
for an average power tool, about 33-35%
(The waste produced in or the consumption of resources in the recycling process is unknown and thus cannot be taken into account in the following figures.)
The primary option, materials recycling (complete reclamation of the iron and nonferrous metals and of the high-quality/high-value plastics after disassembly) is already possible today in the following variants.
3. In the existing shredding systems with prior disassembly:
§ Disassembly of the housing (separation of plastic parts from aluminum parts)
§ Separation of mechanical parts according to pure fractions of each metal
§ Grinding of pure types of plastics and shredding of pure types of metals (iron and copper are separated by magnets, grease and other contaminants are washed away)
Waste reduction by 90-94%
Consumption of resources 6-10% (compared to 1)
4. In shredding systems with flotation separation and partial disassembly:
§ Removal of grease in drive gear
§ Partial disassembly for separation of plastics and metals
§ Grinding of pure materials/shredding of plastics and metals
Waste reduction by 90-98%
Consumption of resources 2-10% (compared to 1)
(Waste volume, consumption of resources, and environmental pollution in the recycling process, e.g., as a result of Cu/Al separation method based on the lead bath, are not taken into account in the above calculations; see Section 1.3, basic strategy 2, materials recycling, absence of recycling technologies.)
Pollutant Emission
The product phases to be compared are
In the actual status In the primary option
a. Collection process Collection process
b. Incineration
c. Dumping in landfills
d. Raw material production Disassembly, recycling, and residual waste
Without more precisely describing these product phases, we can make the following general observations:
a. The primary option may require somewhat more transportation within the country.
b. The pollutant emission during incineration and the costs of avoiding it today are sufficiently known, including the problems of the filter residues from incineration; these do not arise in the primary option.
c. The dumping of power tools, or their incineration waste, or shredding residues in landfills might cause soil and groundwater contamination, although power tools are free of heavy metals; this solution also takes up precious and thus expensive dump volume. Again the primary option looks better.
d. Aluminum (11 wt. %) is very energy-intensive to produce and can be recycled using only 5% of the original amount of energy required. The emissions from the production of iron and steel are at the present state of the art higher than from recycling.
The disassembly of old tools by hand is emission-free. The separation method for the nonferrous metals present in the appliance, copper and aluminum, is based on lead baths and is environmentally suspect. Thus, disassembly and recycling produce fewer pollutant emissions than the present state of affairs.
Summary of Environmental Aspects of the Primary Option
Compared with the actual status, “dumping or incineration,” the primary option, “materials recycling,” has critical advantages in terms of waste volume, consumption of resources, and pollutant emissions. However, it is not (yet) possible to give figures for these advantages, because as far as we know, there are no scientific data available on this, and it is not the task of this study to analyze recycling methods from a technical point of view.
Table 1. A - Technical innovations in the last 10 years
- Plug connections in the electronics (repair-friendly)
- Better cooling of startup limiter resistance by means of installation in fan draft (prevention of breakdown)
- Wear-saving brush holder (prevention of breakdown)
- Dust-protection of bearings by means of double labyrinth with centrifugal force effect (longevity)
- Replacement of asbestos with mica filling in plastics (disposal-friendly
- Motor with divided pole shoe (repair- and disposal-friendly, permits separation of copper and iron during disassembly if screwed instead of welded as today)
- Fan made of plastic with plastic guide ring instead of cast metal (longer life, especially in a sandy environment)
- New quick-fastening system “SOS click,” compatible with power tools made by other manufacturers
Table 1. B - Percentages of materials by weight in product studied (GWS 23-180
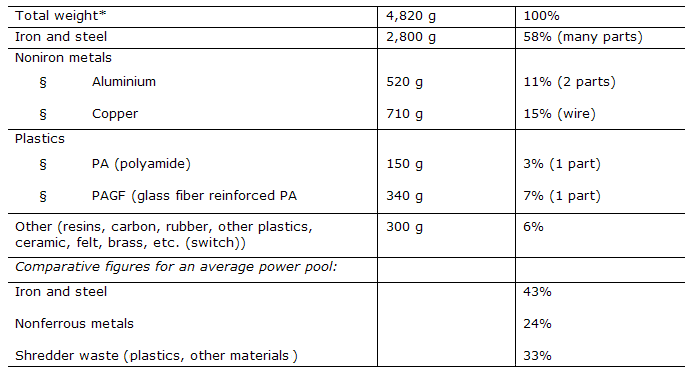
Table 1. C - Options for waste prevention by means of strategies of long-life goods and recycling materials:
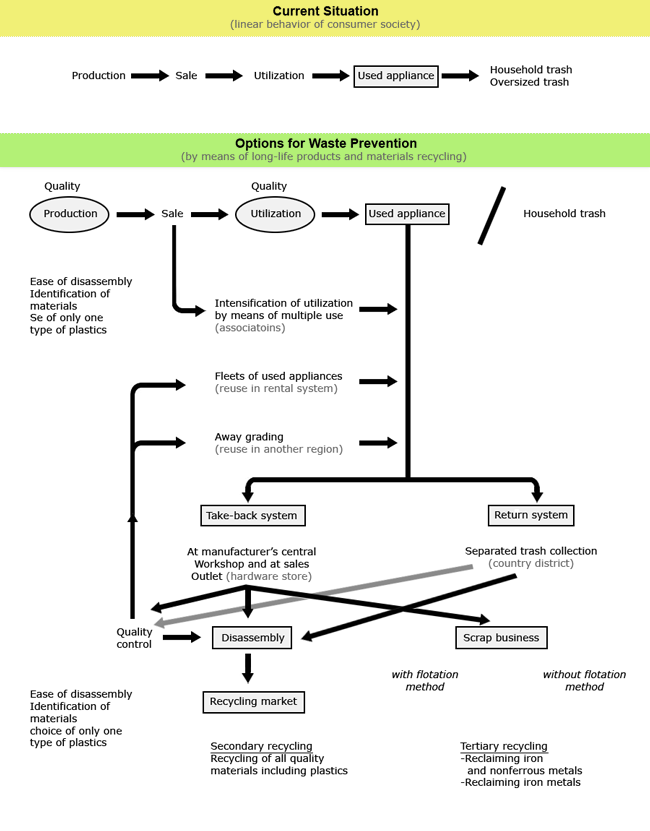